Before delving into the materials, let’s briefly understand what a dual sleeve cone is. A dual sleeve cone is a specialized component commonly found in various industrial applications. It consists of two concentric sleeves, typically made of metal, that are precisely fitted together to form a conical shape. This design offers several advantages, including increased strength, durability, and precision compared to traditional single-sleeve cones.
Common Materials for Dual Sleeve Cones
The choice of materials for dual sleeve cones is crucial to ensure optimal performance and longevity in various applications. The selection process involves careful consideration of factors such as strength, durability, weight, cost, and compatibility with other components.
- Steel: Renowned for its high strength and durability, steel is a popular choice for dual sleeve cones. It offers excellent load-bearing capacity and is suitable for heavy-duty applications in industries such as automotive, construction, and mining.
- Stainless Steel: Possessing superior corrosion resistance and hygienic properties, stainless steel is ideal for environments exposed to harsh conditions, chemicals, or food processing. It is commonly used in the food, pharmaceutical, and chemical industries.
- Aluminum: Known for its lightweight properties and good corrosion resistance, aluminum is often preferred in applications where weight reduction is critical, such as aerospace and automotive.
- Titanium Alloys: Offering exceptional strength-to-weight ratio, excellent corrosion resistance, and high-temperature tolerance, titanium alloys are used in demanding applications like aerospace, marine, and medical industries.
- Copper Alloys: Known for their excellent thermal conductivity and electrical conductivity, copper alloys find applications in heat exchangers, electrical connectors, and other specialized components.
- Nickel Alloys: Offering exceptional resistance to corrosion, oxidation, and high temperatures, nickel alloys are used in demanding environments like the chemical and petrochemical industries.
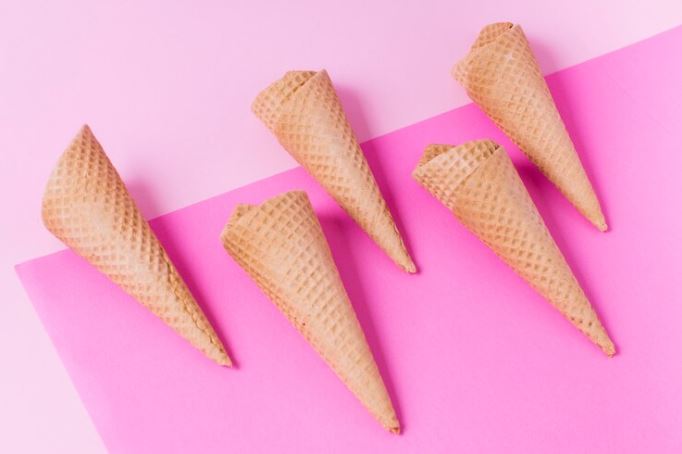
Material Selection Factors
Several factors influence the choice of material for a dual sleeve cone:
- Strength and Durability: The material must be able to withstand the expected loads and stresses without deformation or failure.
- Corrosion Resistance: In environments exposed to harsh conditions, corrosion-resistant materials are essential.
- Weight Considerations: For applications where weight reduction is crucial, lightweight materials like aluminum or titanium alloys are preferred.
- Cost: Material cost is an important factor to consider, especially for large-scale production.
- Compatibility: The material must be compatible with other components in the assembly and the manufacturing processes.
Material Considerations for Specific Applications
The choice of material also depends on the specific application and operating environment. For example:
- Automotive Industry: Steel is commonly used for its strength and cost-effectiveness, while aluminum alloys are preferred for lightweight components.
- Aerospace Industry: Titanium alloys and high-strength steels are used for their excellent strength-to-weight ratio and resistance to extreme conditions.
- Chemical Industry: Stainless steel and nickel alloys are preferred for their corrosion resistance and ability to withstand harsh chemicals.
- Food Industry: Stainless steel is the most common choice due to its hygienic properties and corrosion resistance.
Material Combinations
In some cases, combining different materials for the inner and outer sleeves can provide specific advantages. For example, a steel outer sleeve for strength and a stainless steel inner sleeve for corrosion resistance can create a hybrid component with enhanced performance.
Applications of Dual Sleeve Cones
Versatile Components in Diverse Industries
Dual sleeve cones, with their unique design combining strength, precision, and durability, find applications across a wide spectrum of industries. These components play crucial roles in enhancing the performance and reliability of various systems and machinery.
Automotive Industry
The automotive industry is a major consumer of dual sleeve cones. They are employed in several critical components:
- Suspension Systems: Dual sleeve cones are integral to suspension systems, providing support and absorbing shocks. Their ability to withstand varying loads and vibrations is crucial for ensuring vehicle stability and comfort.
- Steering Columns: These cones contribute to the precision and responsiveness of steering systems. They are designed to handle the forces generated during steering maneuvers.
- Drivetrain Components: Dual sleeve cones find applications in various drivetrain components, such as axles and differentials, where they provide support and transfer power efficiently.
Aerospace and Defense
The aerospace and defense industries demand components with exceptional strength, lightweight properties, and reliability. Dual sleeve cones excel in these areas:
- Landing Gear: These cones are essential components of aircraft landing gear, absorbing the impact of landing and providing structural support.
- Missile Components: Dual sleeve cones are used in missile systems for guidance and control mechanisms, where precision and durability are paramount.
- Satellite Components: In satellite systems, these cones find applications in various components, such as antenna structures and deployment mechanisms.
Industrial Machinery
Heavy machinery and industrial equipment rely on dual sleeve cones for optimal performance and longevity:
- Construction Equipment: Excavators, loaders, and other construction machinery employ dual sleeve cones in hydraulic cylinders, boom assemblies, and other critical components.
- Agricultural Machinery: Tractors, harvesters, and other agricultural equipment utilize dual sleeve cones in various linkages and mechanisms.
- Material Handling Equipment: Forklifts, cranes, and conveyor systems incorporate dual sleeve cones for smooth operation and load-bearing capacity.
Other Industries
Beyond the aforementioned industries, dual sleeve cones find applications in numerous other sectors:
- Oil and Gas: Used in drilling equipment, pumps, and valves, dual sleeve cones withstand the harsh conditions and pressures encountered in the oil and gas industry.
- Marine Industry: Employed in shipbuilding and offshore platforms, these cones offer the necessary strength and corrosion resistance.
- Medical Equipment: Found in medical devices and equipment, dual sleeve cones contribute to the precision and reliability of these systems.
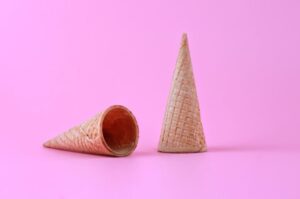
Customization and Special Applications
Due to their versatility, dual sleeve cones can be customized to meet specific requirements of various industries. For example, in the medical field, they might be made from biocompatible materials and subjected to stringent sterilization processes.
In conclusion, dual sleeve cones are indispensable components in a wide range of industries. Their ability to withstand heavy loads, provide precise movement, and ensure durability makes them ideal for various applications. As technology advances, we can expect to see even more innovative uses for these versatile components.
Conclusion
The choice of materials for dual sleeve cones is critical to ensure optimal performance and longevity in various applications. By carefully considering factors such as strength, durability, weight, cost, and compatibility, engineers can select the appropriate materials to meet the specific requirements of each application.
FAQs About Materials for Dual Sleeve Cones
Q: What is the most common material used for dual sleeve cones?
A: Steel is the most commonly used material due to its strength and cost-effectiveness.
Q: What factors influence the choice of material for a dual sleeve cone?
A: Material selection is based on strength, durability, corrosion resistance, weight, cost, and compatibility.
Q: Can different materials be used for the inner and outer sleeves?
A: Yes, combining different materials can provide specific advantages based on application requirements.
Q: What materials are suitable for high-temperature applications?
A: Titanium alloys and nickel alloys are commonly used for high-temperature applications.